WEST LAFAYETTE, Ind. — President Joe Biden signed the CHIPS and Science Act into law on Aug. 9, 2022, authorizing nearly $53 billion to rebuild the nation’s semiconductor industry. With chip factories breaking ground from Syracuse, New York, to Phoenix in the two years since, the focus has grown on how to fill them with the next generation of workers — like Robert Zhang.
The rising sophomore at Purdue University participated in the school’s Summer Training on Awareness and Readiness for Semiconductors (STARS) program, an eight-week intensive program that wrapped up its second summer last month with 100 students, up from around 70 initially.
The initiative, which doesn’t directly receive CHIPS funding, aims to train dozens of undergraduates each summer for domestic semiconductor roles, paying a $10,000 stipend funded by industry sponsors including Intel, GlobalFoundries and Texas Instruments.
STARS will “definitely prepare me and give me the good experience for future opportunities,” Zhang said during his last week of the boot camp, where trainees learn to work in “clean rooms” and labs to either design, manufacture or package their own chips. Hands-on experiences like these are rare outside of graduate programs and paid job opportunities.
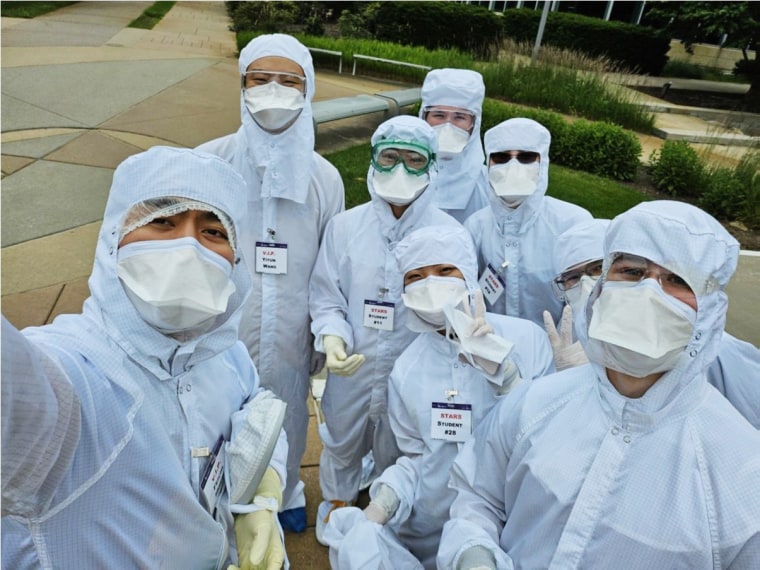
The Purdue program is one of just two monthslong semiconductor initiatives for undergraduates on U.S. college campuses, and the jobs it aims to fill represent just a sliver of the domestic industry’s projected needs.
McKinsey & Co. researchers estimate the U.S. chip sector will still be short 59,000 workers by 2029 even if CHIPS Act-backed programs and funding deliver on their full potential — and up to 146,000 if they don’t. The domestic semiconductor manufacturing workforce has dropped from a peak of 714,500 in 2001 to 392,100 as of July, according to government data.
The Semiconductor Industry Association has already tallied more than $30 billion in CHIPS grants and over $25 billion in loans distributed so far, spanning projects from semiconductor giants like TSMC, Intel and Micron. In addition, the CHIPS Program Office, run out of the Commerce Department, has announced major commitments for research and development, including workforce skilling, with a $5 billion package unveiled in February.
The universities in this country are being asked to triple the number of graduates prepared for careers in semiconductors.
Mark Lundstrom, chief semiconductor officer, Purdue University
Bill Wiseman, a senior partner at McKinsey, sees little risk of the nation’s new chipmaking plants “lying fallow” due to worker shortages. But there is the potential for understaffing to drive up costs, he said, at a time when “operating a factory in the U.S. is already more expensive than it is in the place where most of this demand is coming from, which is Taiwan, Korea, Japan, Singapore.”
One way to shore up the domestic talent pool is to get prospective hires interested early, said Mark Lundstrom, Purdue’s chief semiconductor officer.
“The universities in this country are being asked to triple the number of graduates prepared for careers in semiconductors. So it’s going to take all of us working together to do that,” he said, adding that many existing industry internships come “too late” in students’ academic careers.
Letting undergrads perform parts of the semiconductor development process — like metal deposition, laser cutting and wafer measurement — before their junior year is key, Lundstrom said.
These experiences can help prepare them for jobs in Purdue’s backyard of West Lafayette, Indiana, where South Korean company SK Hynix is planning an advanced packaging facility expected to begin mass production in 2028 — right in time for many STARS participants to enter the workforce. About a quarter of the program’s inaugural cohort went on to secure internships with companies including Apple, Intel, Nvidia and TSMC, Purdue said.
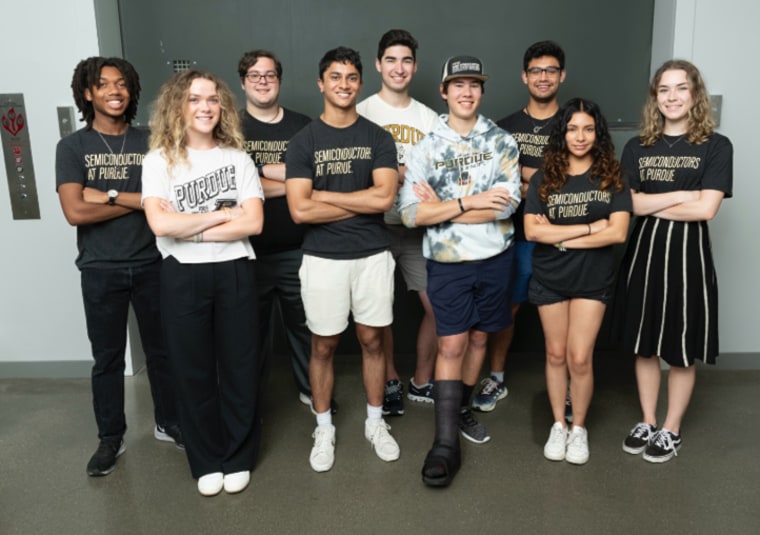
But the industry will need many more job-training efforts to fill the projected talent gap, according to Sujai Shivakumar, a senior fellow at the Center for Strategic and International Studies. Universities and nonprofits, state and local governments, and private-sector employees all have a role to play, he said.
High-wage jobs at U.S. chipmaking plants can help prevent industry talent from going overseas, Shivakumar said, adding that domestic employers would need to offer child care benefits and flexible hours in addition to competitive pay to do so.
“If they don’t come to the United States, they’re going to other nations. Those countries are competing with us,” he said.
The McKinsey researchers proposed a broader range of approaches to fill the talent gap in the meantime, like tapping immigrant communities and military veterans as well as workers with transferable skills in adjacent industries, like pharmaceuticals or automotive manufacturing. The firm also recommends educational institution partnerships, even with high schools, that let prospective hires tour chipmaking facilities or shadow workers on the job.
“Just because you have the courses available, if the students don’t enroll in them, that’s not necessarily going to solve the problem,” said Taylor Roundtree, associate partner at McKinsey.
Lundstrom knows there’s a long way to go and Purdue plays only a small role, but the university wants to do its part. “We just felt we have a responsibility to help the nation address this challenge,” he said.

Brian Cheung
Brian Cheung is a business and data correspondent for NBC News.

Haley Messenger
Haley Messenger is a producer at NBC News covering business and the economy.
Discover more from Tistalents
Subscribe to get the latest posts sent to your email.